The Making of the ORI Strut
By Winston Jones/Times-Georgian Sep 30, 2014
Mark Jensen didn’t start down a career path intending to build parts for off-road vehicles. He was born in Roosevelt, Utah, grew up in northern California and came to Georgia in 1996 to work for Yokogawa in Newnan, an instrument manufacturer.
“My first job had been a Honda motorcycle mechanic,” Jensen said. “I then worked as a machinist and later went to school to study manufacturing engineering.”
It was his hobby experience in off-road vehicles that finally led Jensen and his wife, Marie, to form Off-Road Innovations Inc., a Bowdon manufacturing company that makes struts for those rugged vehicles. The company now employs 16 workers and is flooded with orders from all over the world.
“I had a friend in Utah, who was paraplegic, and he wanted my help in building hand controls for his dune buggy,” Jensen said. “I had been involved in building go karts for my foster boys, and then I built some sand rails.”
One of Jensen’s first sand rails was a four-wheel drive vehicle, with independent suspension, capable of hitting speeds of 100 miles per hour.
“I found that the weakest part of the sand rail was stability,” he said. “I came up with the idea for a strut to cure the problem and got a patent on it.”
In the meantime, the 2001 terrorist attacks had occurred and the downward economy resulted in layoffs at Yokogawa, where he worked.
The Jensens decided to take a risk and go with the strut manufacturing company. Using their own funds, and mortgaging their property, they built a prototype of the strut in 2002 and took it to an off-road vehicle trade show in Arizona.
“After demonstrating it there, we picked up two orders on the spot,” he said.
They first began building the struts in their home in Sharpsburg, as a family project, with their children helping with the work. They contracted with machine shops to build the components and assembled the finished product in their home shop.
When it became apparent that they needed to machine their own parts, they found the building at 200 Campbell Avenue in Bowdon for a good price. It had been a tool and die shop for the nearby Carlisle Tire plant, which had been destroyed by fire.
The factory makes the ORI Strut, a dual-pressurized, off-road vehicle stabilizer that comes in stroke lengths from 6 to 30 inches, and is an industry leader. Prices start around $750 each. They’re used around the world on sand rails, rock crawlers, modified Jeeps and monster trucks.
“We’re a made-in-the-U.S.A. company,” Jensen said. “Everything is done here in the Bowdon plant except for the color anodizing.”
Jensen said all parts also come from the U.S., except for a small bearing, which is made in China. Most competitors outsource the majority of their work, he added.
“The reason we’re buying the bearing from China is because we found U.S. suppliers hard to work with,” he said. “They could never supply us with enough, and we couldn’t keep it in stock. It’s very expensive.”
He said the Bowdon factory is styled on the Toyota production system, with the plant producing about six struts per day. The work begins with raw materials, such as steel bar, and ends with assembly and testing of the finished product. Workers earn bonuses by meeting incentive production goals.
“The ORI strut offers a lot of features in a small package,” Jensen said. “It’s nitrogen gas filled and has no mechanical springs. It offers roll stability due to dual pressurized gas chambers.”
“Most of our marketing has been by word of mouth,” said Marie Jensen, who is the company vice president and financial officer. “We have not run magazine ads and only attended one trade show. We have a good product, and when they see how it reacts on the side of a mountain, providing a soft, stable ride, they’re ready to buy. At this point, we’re completely out of debt and have done it all on our own money.”
“Early on, a financial adviser told us we could only make it with venture capital,” Mark said. “Well, we’re still here and growing, and we did it without venture capital.”
Mark is the president/CEO of the corporation. Liz McIntosh is the office manager.
Most of the Jensens’ seven children have a role in the company, except for the oldest son, who is an Atlanta police officer; the youngest, who is not yet old enough to work in the factory; and daughter, Sarah, who is an art major at Brigham Young University.
Son Russell handles the website and marketing. Kirk, who will graduate next year with a degree in auto engineering, handles tech support. Daughter Carissa handles safety matters and does graphic arts work, including a new company sign, which will soon be installed on the building and company logo T-shirts. Son Nolan does general labor in the factory.
Mark said the biggest challenge to the industry is finding a good workforce. He said it’s sometimes difficult to interest young people to seek jobs in manufacturing.
However, he noted that manufacturing jobs of today are not like those of past years. He said manufacturing work is mentally challenging.
“Everything is run by robots,” he said. “You have to have computer skills to program machines and know how to maintain them.”
Mark said all work is honorable, whether white or blue collar.
“Right now, we have a good team,” he said. “But a skilled workforce is hard to find. Nobody coming right out of college can come in and hit the ground running. We train them and pay them well.”
Mark said a good work ethic is also vital in manufacturing.
“That’s the kind of people we’re looking for, people with a good work ethic,” he said. “We do random drug testing, out of necessity, not because we want to be mean. If workers are on drugs, their reflexes slow and they can do thousands of dollars of damage to equipment, which causes downtime to repair.”
Mark said doing the work you love is the most important factor and the key to happiness in a job. He, himself, left a cubicle job for the manufacturing world.
“I’d rather be out on the floor, doing something,” he said.
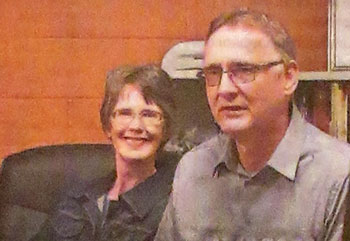
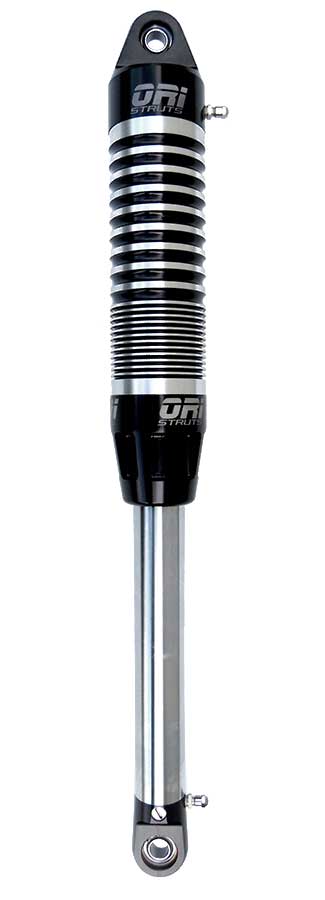